Fasteners and Machining: Tailored Solutions for every single Manufacturing Requirement
Wiki Article
Navigating the Globe of Fasteners and Machining: Techniques for Precision and Rate
In the detailed world of fasteners and machining, the quest for accuracy and rate is a continuous obstacle that demands thorough attention to information and tactical planning. From recognizing the diverse array of bolt types to choosing ideal materials that can stand up to extensive demands, each step in the process plays a critical duty in attaining the wanted result.Understanding Bolt Kind
When picking fasteners for a job, recognizing the various types readily available is important for making certain optimum efficiency and integrity. Bolts are utilized with nuts to hold products with each other, while screws are flexible bolts that can be used with or without a nut, depending on the application. Washers are essential for distributing the load of the fastener and avoiding damage to the material being attached.
Picking the Right Products
Recognizing the relevance of picking the right materials is critical in making certain the optimal efficiency and reliability of the selected bolt kinds reviewed previously. When it pertains to bolts and machining applications, the product selection plays an essential duty in establishing the general toughness, resilience, corrosion resistance, and compatibility with the desired environment. Different products provide differing homes that can considerably impact the efficiency of the fasteners.Typical products utilized for bolts include steel, stainless steel, light weight aluminum, brass, and titanium, each having its one-of-a-kind toughness and weak points. Steel is renowned for its high toughness and sturdiness, making it ideal for a wide variety of applications. Selecting the ideal material entails considering aspects such as stamina needs, environmental problems, and budget plan restrictions to make sure the wanted efficiency and long life of the fasteners.
Accuracy Machining Techniques

Along with CNC machining, various other precision techniques like grinding, turning, milling, and exploration play important duties in fastener manufacturing. Grinding assists attain fine surface coatings and tight dimensional resistances, while transforming is often utilized to produce round components with specific diameters. Milling and drilling procedures are crucial for shaping and producing holes in bolts, guaranteeing they meet precise specifications and feature appropriately.
Enhancing Speed and Efficiency
To optimize bolt manufacturing procedures, it is necessary to streamline operations and execute effective strategies that match accuracy machining strategies. One crucial technique for boosting speed and performance is the application of lean production principles. By minimizing waste and focusing on constant improvement, lean methods assist optimize and eliminate bottlenecks operations. Additionally, spending in automation technologies can dramatically enhance manufacturing speed. Automated systems can take care of repeated tasks with precision and rate, allowing employees to focus on even more complex and value-added tasks. Taking On Just-In-Time (JIT) stock monitoring can likewise enhance performance by making certain that the ideal materials are available at the correct time, minimizing excess inventory and reducing preparations. Cultivating a society of collaboration and communication amongst group participants can boost overall effectiveness by advertising transparency, analytic, and innovation. By combining these techniques, suppliers can attain an equilibrium between speed and accuracy, inevitably improving their one-upmanship in the bolt market.Quality Assurance Measures
Implementing rigorous quality control procedures is crucial in ensuring the integrity and consistency of bolt products in the production process. Quality assurance steps incorporate various phases, beginning with the choice of basic materials to the final assessment of the completed bolts. One basic element of high quality control is conducting detailed material evaluations to verify compliance with specifications. This involves assessing variables such as product strength, durability, and make-up to guarantee that the fasteners fulfill market requirements. In addition, keeping track of the machining processes is necessary to support dimensional accuracy and surface coating high quality. Making use of innovative modern technology, such as automated inspection systems visit and accuracy measuring tools, can enhance the accuracy and efficiency of quality assurance procedures.Regular calibration of equipment and equipment is imperative to preserve uniformity in production and ensure that bolts satisfy the required tolerances. Implementing rigorous methods for identifying and resolving flaws or non-conformities is important in protecting against substandard products from entering the market. By establishing a thorough quality assurance structure, manufacturers can copyright the online reputation of their brand and provide fasteners that fulfill the highest possible standards of efficiency and sturdiness.
Final Thought
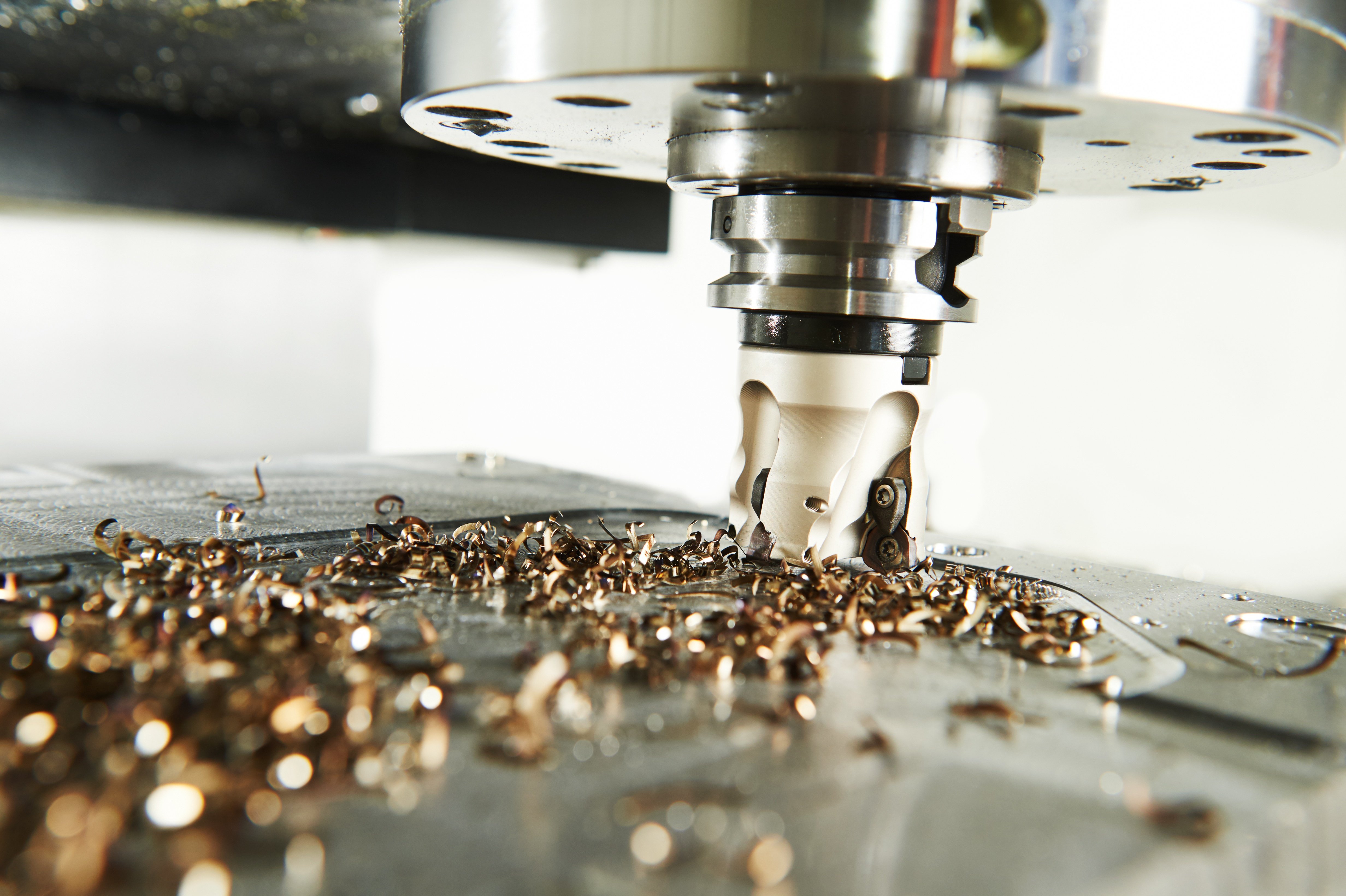
In the elaborate realm of fasteners and machining, the mission for accuracy and rate is a perpetual difficulty that requires meticulous attention to detail and tactical preparation. When it comes to bolts and machining applications, the material selection plays a critical role in establishing the total toughness, durability, deterioration resistance, and compatibility with the desired atmosphere. Precision machining entails numerous advanced approaches that make certain the tight tolerances and specifications needed for fasteners.In addition to CNC machining, other accuracy techniques like grinding, transforming, milling, and drilling play vital roles in bolt manufacturing.To maximize bolt production procedures, it is essential to simplify operations and implement efficient methods why not try this out that match precision machining techniques.
Report this wiki page